What does the Industrial Internet of Things (IIoT) mean to you?
As a manufacturer, it gets right to the core of our business and operations. Technology that brings our three primary groups – IT, Industrial Controls, and Operations – closer together is going to make fundamental changes to the organization. It’s a great time for IT to become an even stronger partner to the business by leveraging what we do best in a space that is ripe for new ideas.
Here at Inteva, the Operations group is responsible for producing everything that the company’s reputation is built on. Each plant has their own P&L, so each site is laser focused on efficiency. This team is built around ensuring that people, processes, and technology are performing standard work so that the one millionth part produced is exactly like the first.
The Industrial Controls group is focused on bringing in new equipment to the plants, such as injection molders, welders and laser cutters, all of which can be major expenses, and must be used over many years. They end up with a number of system requirements to access these devices and Programmable Logic Controllers (PLCs), and many versions of operating systems and applications to support equipment that may be in service for several decades.
Our Corporate IT group is built primarily around business analysis. Our infrastructure teams are relatively small for a company our size so that we can focus on providing systems expertise around logistics and production control – the areas where we make (or lose) money based on efficiency. We also focus on the interface between the PLC and the ERP system. These Manufacturing Execution Systems (MES) and operator interfaces enable part management and sequencing.
The changes we’ve seen over the past couple of years are focused on improved traceability, improved production control techniques, more custom finished goods, and product quality. This is where the IIoT concepts and technical options have played well.
IIoT for Tracing Materials and Personnel
When we think of traceability, we tend to focus on material going into the product. With our production processes, we often turn raw plastic pellets into a finished interior auto part. If there is ever an issue, we want to be able to trace back to determine the root cause. Tying the production equipment to the raw material to the completed component can only be accomplished by more aggressive use of IIoT technology – from input sensors on plastic silos to ensure the right material is used, to gauges and monitors ensuring operating parameters are within target.
Additionally, we’ve been working to add personnel tracing to this. Network improvements and low-cost sensors/input devices are allowing us to better manage the overall plant to ensure that the appropriate, trained personnel are building parts. We can’t train everyone on every process, so labor scheduling is a vital part of production planning. Technology is driving the operator interface to the point where the operator must login to a work center where the system determines if that operator has been certified to do perform this process. In some locations, we are taking the systematic steps to shut down the equipment if the operator is not certified. While this may not be considered IIoT technology, the idea of driving traceability and management to all portions of the process is evidence of how thoroughly we are embracing the concept.
Improving Production Control
We’ve also been working extremely hard in the area of improved production control techniques. Simple AI application of pattern matching and computer-based camera and sensor inspection is going a long way toward improving components and finished goods. With our advanced cut, sew, and wrap operations, we are visually inspecting parts using systems to ensure quality before moving to the next step – taking subjective human inspection out of the equation.
Most of the products we deliver to our customers have become much more customized. Colors, fabrics from plastic to leather, and a number of other options drive customization into the mass production line. Only with system controls and production management can this variability of finished goods be achieved.
Related article: Combine IIoT and Industry 4.0 for Competitive Advantage by Martin Davis |
Deploying IIoT for Quality Assurance
The final area that IIoT has impacted significantly for us is product quality. In some processes, for example, we must enforce an exact time that an adhesive has to set before it goes to the next step. Previously, this had been manually managed. As we’ve taken this into systems, we restrict a product moving to the next step before it is ready. As products may be moving between process groups, this is critical. While one group may be able to manage steps within their process, it’s impossible when the other group may be on the other side of the facility. With our system controls, we can lock the part into a status that isn’t released until the timing is met. Attempting to scan a part into the next step too early will result in an error notification and potential line stoppage.
Another area that IIoT is helping with in product quality is the monitoring and managing of production equipment. We use an AI based tool to visualize production results and the large number of variables that were present during that production. Over time, the specifications for tolerance can be narrowed as the system determines which parameters should be adjusted based on raw material, equipment performance, and environmental conditions. Incorporating these tools is not simple, it requires a major focus by the operations and maintenance teams to create check-sheets to identify our parameters. This upfront work will generate major long-term payback. For instance, waste and scrap are two areas of profit improvement that fall right to the bottom line.
There are a huge number of technologies and techniques that are going to impact the production floor over the next couple of years. 5G and other improvements in network connectivity to reduce latency and make the shop floor a real time environment will drive many new solutions. The goal is to start thinking about the needs now so that you can leverage solutions as they mature. The communication between the groups involved is critical and should begin now!
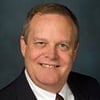
Written by Dennis Hodges
Dennis Hodges is CIO of Inteva Products, a $1.5 billion auto parts manufacturer based in Troy, MI. He has held the position since 2007.